セラミックス材料・デバイスのエキスパート
全固体電池開発に挑む
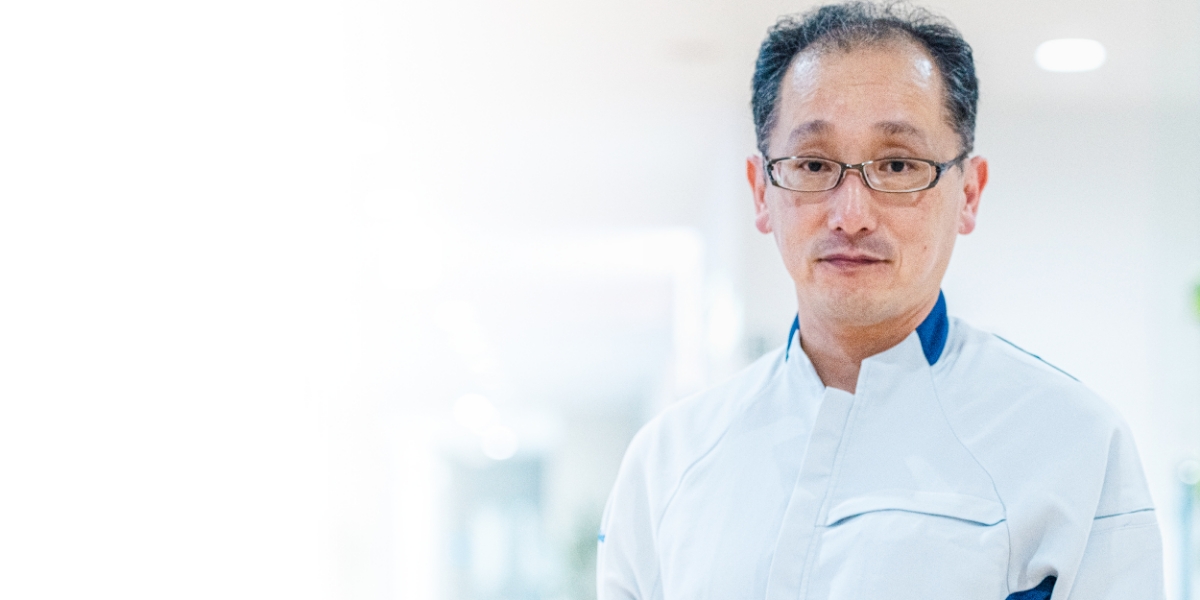
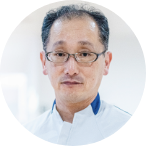
専門:セラミックス材料・プロセスと応用デバイス
テクノロジー本部 マテリアル応用技術センター
材料開発から量産までの一気通貫を経験――、社内でも珍しいキャリアを積んできたセラミックのスペシャリストが古賀英一さんです。「自分の開発した材料は量産化までやりたい、そう思って仕事を続けてきました」と言う古賀さんは、量産までの各プロセスを経験しながら開発に打ち込んできました。シニアリサーチャーとして現在取り組んでいるのが、EVの車載業界などから注目を集めている次世代のバッテリー、全固体電池の開発です。技術確立・量産化に向けて取り組む古賀さんに、仕事のやりがいや日々の働き方について聞きました。
*高度専門職…パナソニック ホールディングス株式会社では、高い専門性で活躍する技術者を対象に、専門性を評価し活躍を後押しすることで技術による価値創出強化を目指す「高度専門職制度」を2015年から導入。
材料・デバイス、プロセスの視点から考える
全固体電池で使用する固体電解質という材料の合成を担当しています。一般的な電池はプラスとマイナスの両極の間を有機溶媒で作られる液体の電解質で満たして電流を生みます。一方で、全固体電池は電解質に固体を使用するバッテリーを指し、液体を使用せず構成要素がすべて固体なので全固体電池と呼びます。
エコロジーの観点からEV車の普及が急がれていますが、現在使用されているリチウムイオン電池は引火性の高い液体の有機溶媒を電解質に使用しているため、激しい発熱が生じると発火事故につながりかねない可能性があります。より安全性の高い電池として全固体電池の開発競争が世界的に激化しています。
パナソニック ホールディングスが開発を続けているのが、固体電解質の素材として耐熱性に優れる広義でのセラミックスです。私が全固体電池の担当を始めた当時は積層プロセスを担当しており、2年前から材料合成の研究開発をしています。セラミックスで作るMLCC(Multi Layer Ceramic Capacitor)に代表される積層デバイスは、例えばミルフィーユのように薄い膜を積み上げていくものが主流で、材料合成で作った生地を積層プロセスで重ねて形を作っていくイメージです。まだ、誰も実用化していない全固体電池の開発は、これまでとは全く異なるアプローチが求められており、日々研究を行っています。
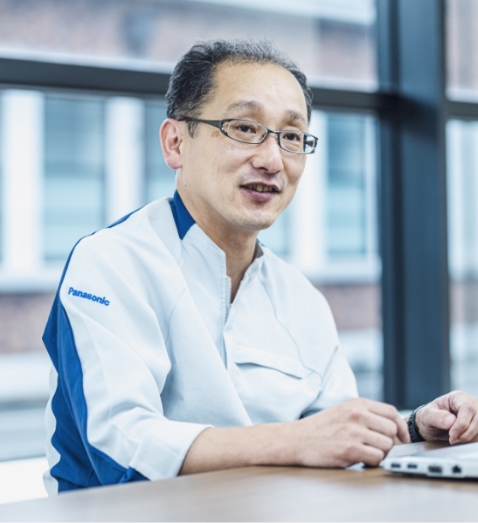
開発した新しい材料を量産しようとすると、よく不具合が起こります。でも、自分が開発した材料が「量産できません」と言われてしまうと悔しい。私は材料を携えて生産拠点である北海道に移り、量産ラインの立ち上げも何度か担当したことがあります。
そこで「量産の段階まで、しっかり考えていなかった」と反省。もちろん最終の製品をイメージして開発はしてきたのですが、量産現場に立ってみると、景色が変わります。技術者のみなさんには、機会があれば、モノを売る一歩手前の工程である量産現場に足を運んでもらいたいと考えています。もちろん研究開発も大切ですが、企業にいる者としては、世の中に出すことが一番ですからね。
失敗から学んだ技術者としての基本
材料の合成から製品の製造まで、セラミックスの長い製造工程の全てに携わった経験だと思っています。また、研究開発から量産化まで、広範な経験も大きな強みだと考えています。試作レベルならば、1人で材料の合成から積層、焼成までこなして、セラミック部品を作ることができます。
セラミックス製品には多くの工程があり、工程ごとに高度な技術を含む長いプロセスが必要ですが、今は分業が一般的なので知識としては持っているけれども実際に自分で全部できる、という人が少なくなっています。例えば、材料製造では、最初の最初にセラミックスの粒子と水を混ぜた「スラリー」というどろどろの生地を作ります。お湯に粉末スープを溶かしたような状態です。粉末は満遍なくよく溶かす必要があるので、通常は分散剤を使用しますが、その時にナトリウムが含まれた分散剤を選択すると、耐湿性能が大きく低下することがあります。この分散剤の選択が後に影響する場合があります。確かに粉末はよく溶けるので、スラリーを作る工程だけを考えれば使いやすいのですが、最終的な製品のイメージを持たないと後工程の担当者が苦しむことになります。これは極端な例ですが、この後しかし、自分たちが作った材料がどういう工程を経て、どういう用途で使用されるデバイスになるのか、セラミックスの技術者は把握しておかねばなりません。開発者が一番新材料の知識を持っているので、その知見を次につなげると量産まで全体のスピードが大きく違ってくると思います。
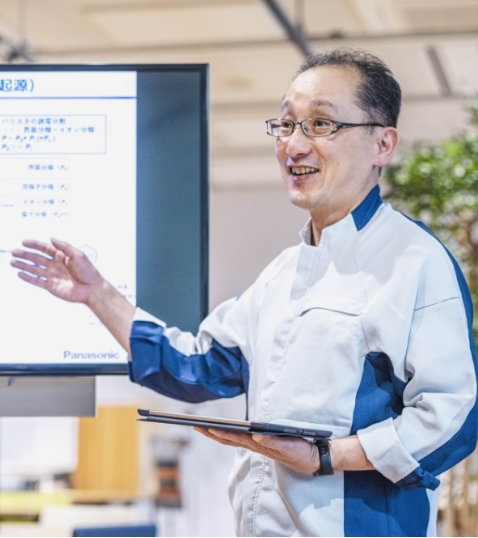
自分が担当した商品でロットアウトを連発し、一時的に出荷できないという事態を引き起こした経験があります。その時、送られてきたデータを確認していたのですが、品質管理の責任者から「なぜ現物を自分で確認しないのか」と言われたことを今でも覚えています。
ハッとしました。当たり前ですが、送られてきたデータを見るのと自分で不良品を確認するのとでは全く違ったんです。起こっている現象から分析しなければ、材料や設計、プロセスのどこに問題があるのか見つけるのは難しい。目の前の事象をきちんと確認して、材料・プロセス・デバイスにいたる視点から巨視的に分析を心掛ける、技術者の基本を改めて学びました。また、現場のみなさんはじめ、多くの方に尽力していただいて、ミスをなんとか挽回したことも忘れません。1人でモノづくりをしているわけではない、いろんな人たちと協力しながらやっていると、深く実感した経験です。
外部との交流、技術の継承も
私も含めて、技術者の中には「新しい技術開発に取り組みたい」「専門性を極めていきたい」と考える人が多いので、専門職という選択肢はとてもありがたいポジションです。管理職と求められる資質が異なりますし、個人が持つ資質にあった働き方です。しかし、管理職のように人と接する必要がないかというと全くそうではありません。特にプロセスが細分化されて分業化されているセラミック分野では技術開発は1人で成し遂げるものではなく、技術だけでなく、生産技術や製造部門など、いろいろな方々の協力をいただいて、形にしていく必要があると思います。
専門職に任命されても同様です。技術開発に専念するだけでなく、薄膜から厚膜に渡る材料プロセス系技術者を対象とした研究会の運営を行っています。全社横断的な会で約70人が所属、技術で困ったことを相談しあったり、外部から講師を招いてセミナーを開いたりと皆のつながりや、研鑽の場になっています。また、以前に所属していた部署からの技術協力要請にも、積極的に協力するように心掛けています。
*高度専門職…パナソニック ホールディングス株式会社では、高い専門性で活躍する技術者を対象に、専門性を評価し活躍を後押しすることで技術による価値創出強化を目指す「高度専門職制度」を2015年から導入。
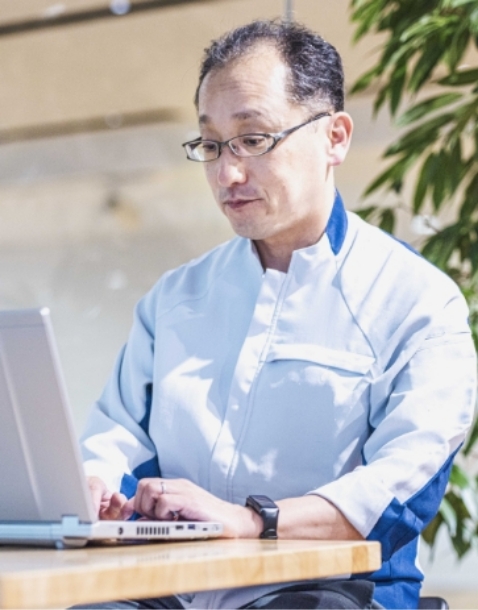
論文を提出すれば立場や声の大小に関係なく、第三者である業界の専門家が客観的に査読してくれますし、発表すれば問い合わせやコメントをいただける。普段はなかなか聞けない貴重な意見をいただける機会だと思って大切にしています。専門書を開いて勉強するのは、エネルギーが必要ですが、雑談の中で技術の話をすると不思議と頭に入ってきますよね。特に自分の専門外のことは、その道の専門家に教えてもらった方がいいと思っています。そうして周りとつながっていけば、自分たちがよく知らないことに対して、誤った情報などで、間違ったことをしてしまうことを減らせるのではと思っています。
コツコツやれば、技術が残る
コツコツとやること、材料・デバイス・プロセスの視点から考えることです。セラミックスにおいては材料の成り立ちや多くの工程、長い製造プロセスが、現象を複雑にするので、どこかで技術の継承が途絶えてしまうとそのままになってしまう可能性が高いと思います。どんなに細々とでも、研究を続けることが次の世代につながっていきます。また、論文執筆や特許出願書類の作成業務は特に地道にやっていくことが大切だと思います。私は毎日少しずつでも書くことを心掛けています。毎日100字書けば、大体2カ月あれば1本の論文が仕上がります。続けていけば、継続して知識を残していくことができます。論文や特許をまとめると、現在までに世の中で確立された技術と、新しいこと、その境界をきちんと認識でき、普段の技術開発の役にもたちます。
To the Next
先人の積み上げた技術に、自分の技術を加える
全固体電池に関しては、技術を確立して最終的に仕上げるところまで、どうにか持っていきたいと思っています。チャレンジングな開発ですが、全固体電池で培ったプロセスは他の分野でも生きてくるはずなので、コツコツと積み上げていきたいです。驚くような新材料や誰も作れなかったデバイスを作りたいという想いはもちろんあるのですが、本当のことを言うと、自分の技術が部分的にでも使われている製品が多くの人の役に立っていればそれだけでうれしいと思います。これまでの方々が築いた技術があって、その上に、新しいことを加えていく、ということが自分は大切だと思っています。だから私の研究を後輩が引き継いで磨き上げて形にしてくれてもうれしいです。